Multi-Chamber Animal Cremation UnitKMA 1200-1000 4C
90 min / 75 lb/hr/chamber (100max) – 400 lb Capacity
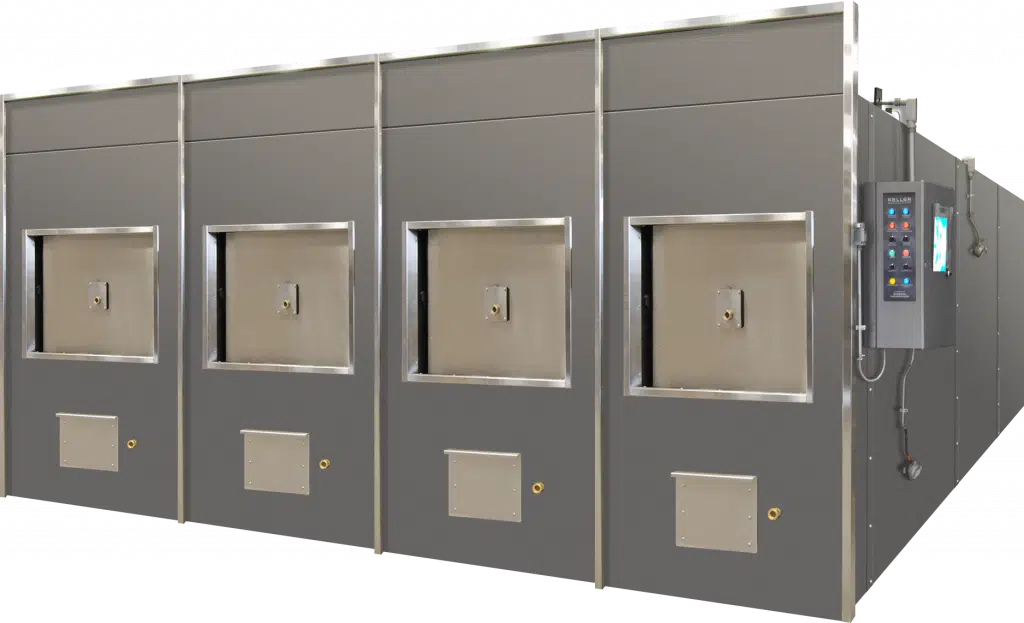
The KMA 1200-1000 4C model is our high volume, high capacity four-chamber animal cremator offering flexibility, performance and equipment features not found in any other unit of its class. Manufactured to meet your needs at a capacity of 400 lbs. per cremation cycle and a burn rate of 75 lbs/hr per chamber (100 max), this model can complete single or multiple cremations every 90 to 120 minutes – making it ideal for mid to high volume veterinary facilities.
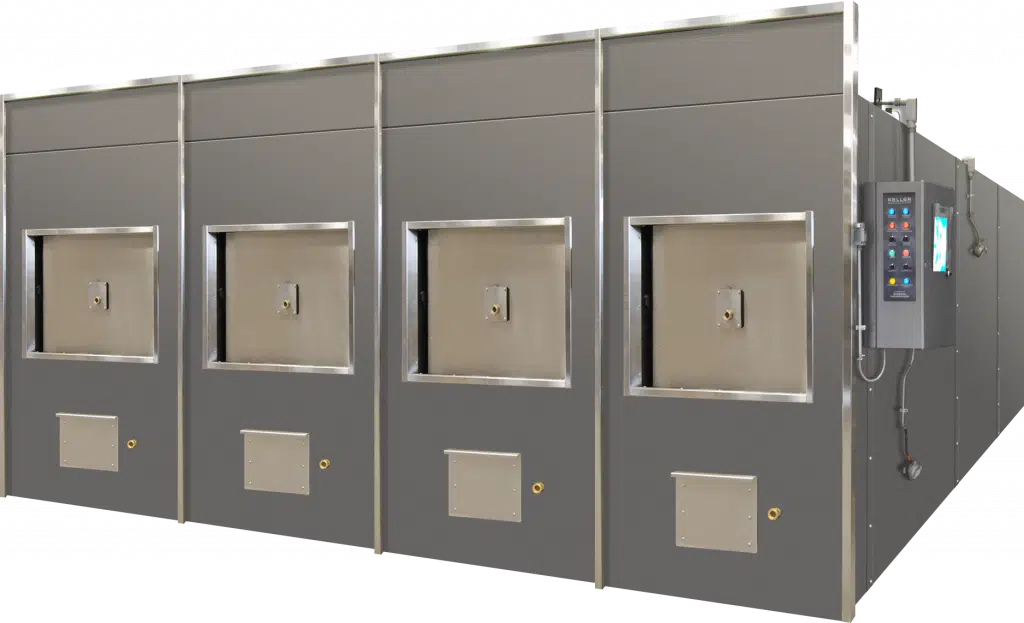
Equipment Overview
The KMA 1200-1000 4C model is our high volume, high capacity four-chamber animal cremator offering flexibility, performance and equipment features not found in any other unit of its class. Manufactured to meet your needs at a capacity of 400 lbs. per cremation cycle and a burn rate of 75 lbs/hr per chamber (100 max), this model can complete single or multiple cremations every 90 to 120 minutes – making it ideal for mid to high volume veterinary facilities.
- Unrivaled output – minimal cooldown between cremations
- 24 Hr. continuous operation – 38 ⅞” wide cremation chamber
- Cremate 75 lbs/hr per chamber (100 Max) (400 lbs total) (34 kg) per cremation cycle (45.4 kg max)
- A complete cremation every 90-120 minutes
- Entirely automatic PLC operating system with redundant controls
- Pollution control system eliminates visible emissions
- Advanced combustion air distribution system with over-fire air
- Observation port for all chambers
- Cast refractory lining through entire machine
- 3,000 °F castable refractory “Hot Hearth”
- Refractory lined stack and draft reducers
- Powder coat paint finish with stainless steel trim
- Primary and Secondary digital temperature displays
- Secondary chamber temperature recorder – standard
- 10” color touch screen with redundant manual control panel
- Cremation chamber loading/clean-out door
- Tools: Steel wire brunch and rake with long handles and short handle rake.
- Virtual service capable
- One year limited warranty
- O2 monitor control system for maximum efficiency
- Larger touch screen
- Full stainless steel outer skins
- Data acquisition
- Integrate control system into clients network
- Unrivaled output – minimal cooldown between cremations
- 24 Hr. continuous operation – 38 ⅞” wide cremation chamber
- Cremate 75 lbs/hr per chamber (100 Max) (400 lbs total) (34 kg) per cremation cycle (45.4 kg max)
- A complete cremation every 90-120 minutes
- Entirely automatic PLC operating system with redundant controls
- Pollution control system eliminates visible emissions
- Advanced combustion air distribution system with over-fire air
- Observation port for all chambers
- Cast refractory lining through entire machine
- 3,000 °F castable refractory “Hot Hearth”
- Refractory lined stack and draft reducers
- Powder coat paint finish with stainless steel trim
- Primary and Secondary digital temperature displays
- Secondary chamber temperature recorder – standard
- 10” color touch screen with redundant manual control panel
- Cremation chamber loading/clean-out door
- Tools: Steel wire brunch and rake with long handles and short handle rake.
- Virtual service capable
- One year limited warranty
- O2 monitor control system for maximum efficiency
- Larger touch screen
- Full stainless steel outer skins
- Data acquisition
- Integrate control system into clients network
Frequently Asked Questions
Yes. Upon notification from the customer that the installation is complete, a Keller technician will travel to the facility to place the unit in operation. Our technician will spend up to three days at the site curing the refractory lining of the cremator, starting up the unit, adjusting air and gas settings and proving all systems. To complete the start-up the technician will perform a cremation and train crematory personnel in the simple operation. It is important that a cremation be available for training at start up.
We warrant our equipment to be free of defects in workmanship for one year and our staff is available around the clock to provide technical assistance and operating support. The Operating & Maintenance Manual describes the function of all components and is invaluable for troubleshooting. We stock a complete line of replacement parts and major components and our Service Department is available for service and repairs on all makes of cremation equipment.
Standard to the KMA-1200 line of animal cremators is a proven and tested automatic operating system with color touch screen control. Load the body and container in the primary chamber, set the timer and press the Start button to begin the cycle. The system is programmed to begin a 45-second purge cycle before igniting the secondary chamber burner to start the preheat cycle. Once the proper temperature is reached in the pollution control chamber, the primary burner is ignited to begin the cremation cycle. Upon completion of the cremation the system advances to the cool down cycle at which time the burners shut down and clean out of the cremated remains can be made.
Complete combustion is achieved in the KMA-1200 line’s temperature-controlled large secondary chamber. Greater than 99% of volatilized carbon created in the combustion process is converted to carbon dioxide. In addition, an Opacity Sensor is located at the base of the stack to monitor the clarity of the exhaust gases. Once the exhaust gases reach 20% opacity, the PLC automatically shuts down the primary burner and adjusts combustion air supply to slow the combustion rate and prevent visible emissions from exiting the stack.
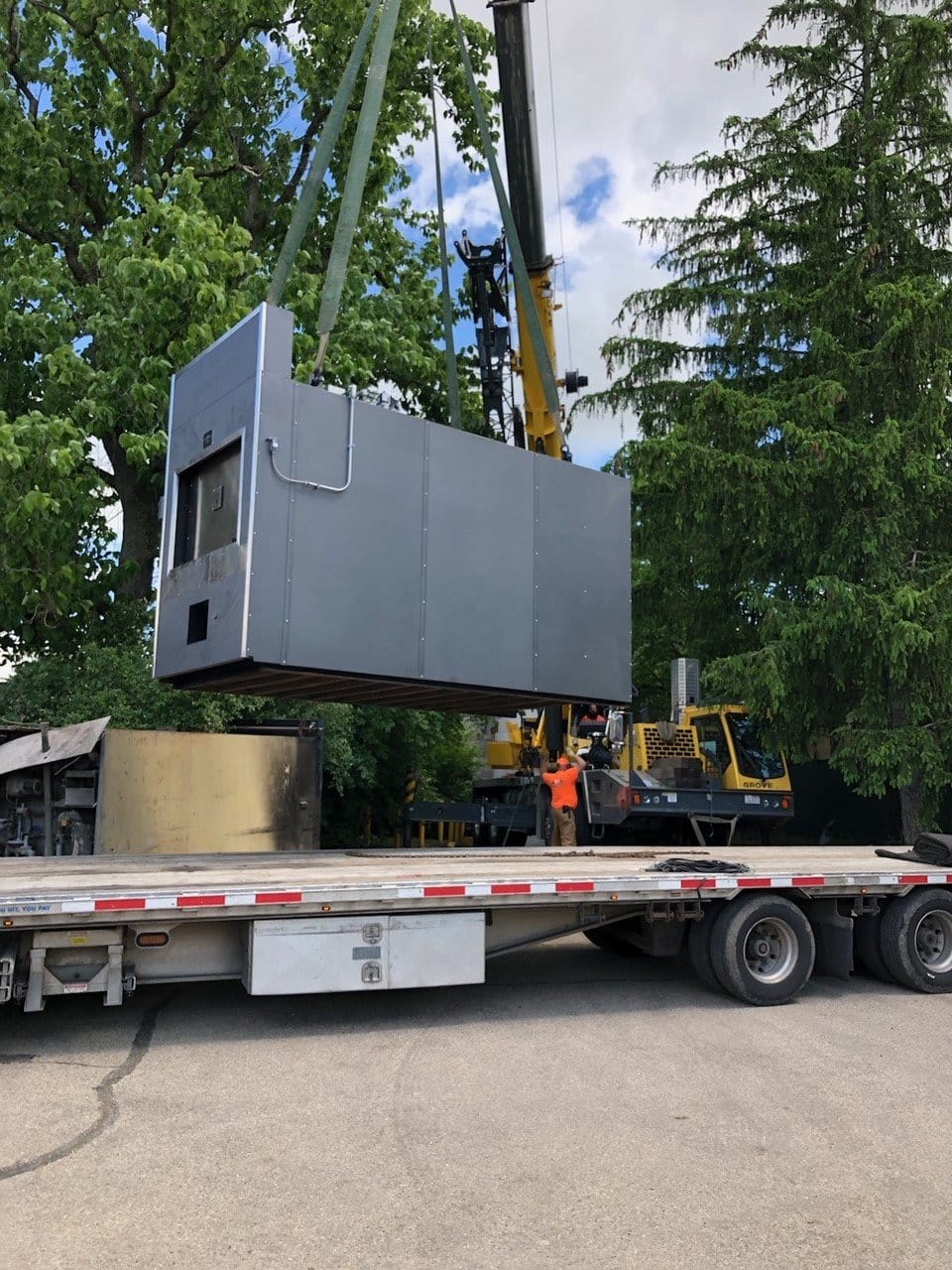
Ready to Get Started?
Coordinate with our expert staff on your facility’s requirements.
Equipment Specifications
Performance Features | |
---|---|
Cremation Cycle Time | 90-120 min |
Burn Rate | 75 lbs/hr/chamber (100 Max) |
Capacity (Single Load) | 400 lbs |
24 Hr. continuous operation
Heavy-duty insulation and state-of-the-art drafting allows for continuous operation, no cool-downs between cremation cycles. |
|
Automatic PLC Operating System
The cremation cycle is controlled by a programmable logic control (PLC) system for complete automation from start to finish. |
|
Redundant Controls | |
Pollution Control System
Complete combustion is achieved in the Pollution Control Chamber, eliminating smoke and odor. All Keller Manufacturing cremators meet or exceed federal, state/province and local environmental regulations. |
|
Advanced combustion air distribution system with over-fire air | |
Standard Equipment Features | |
Observation port for both chambers | |
Cast refractory lining through entire machine | |
3,000°F castable refractory “Hot Hearth” | |
Refractory lined stack and draft inducers | |
Powder coat paint finish with stainless steel trim
The top and rear compartments are finished with two coats of high-temperature, textured, black polyurethane. The front and side panels are powder coated in a claret color. The cremator is trimmed in stainless steel. |
|
Primary and Secondary digital temperature displays | |
Secondary chamber temperature recorder | |
10” color touch screen with redundant manual control panel
Visual confirmation of the system status is provided through a Color Touch Screen Panel which displays temperatures, elapsed time, burner operation and other functions. Continuous fuel and air modulation is automatically controlled by a time/temperature actuated system. Operator interface performed through the Color Touch Screen. A Temperature Chart Recorder (if applicable) is provided. |
|
Virtual service capable | |
Warranty | One year limited |
Safety Certifications
Keller Manufacturing cremation units comply with nationally recognized safety standards and have been tested and listed by Underwriters Laboratories, Inc. (UL) |
|
Service and Support | |
Annual Evaluation and Maintenance (AEM) | Optional |
Control & combustion upgrades | Optional |
Equipment Installation | Optional |
Equipment Commissioning | Included |
Operator Training | Included |
Optional Upgrades | |
O2 monitor control system for maximum efficiency | Optional |
Larger touch screen | Optional |
Full stainless steel outer skins | Optional |
Data acquisition | Optional |
Integrate control system into clients network | Optional |
Specifications | |
Equipment | Multiple Chambered Animal Cremator; Natural Gas, Propane (LP) or Oil fired. |
Construction Standards
The cremator shall be constructed of U.L. /CSA listed components and will meet or exceed nationally accepted incinerator construction standards as originally established per the Incinerator Institute of America (IIA) publication guidelines |
|
Cremator Dimensions | |
Chamber volumes: | Primary - 160 ft3 (4.53 m3) total / 40 ft3 (1.13 m3) per chamber / Secondary - Primary - 180 ft3 (5.09 m3) Note: Primary Chamber Volumes are figured on the chamber only. Does not include chase-way behind the chamber. |
Primary Chamber: | 52 ¼" L x 38 ⅞" W x 35" H (1327 mm x 988 mm x 889 mm) |
Structural footprint: | 97" L x 217 ¾" W (2464 mm x 5531mm) |
Over-all dimensions: | 109” L x 222" W (incl. Touch Screen Panel) x 113.31 H (2769 mm L x 5639 mm W [W/Touch Screen Panel] x 2878 mm H) |
Power Charging Door | |
Door Width | 36” (914.4 mm) |
Door Height | 36” (914.4 mm) |
Primary Chamber Opening | |
Width | ? |
Roof Arch Height | ? |
Operating Temperature
Temperatures are determined as a result of federal, state or local permitting authority operating standards. |
|
Typical primary chamber setting | 1,000ºF-1,600ºF (538ºC - 871ºC) |
Typical secondary chamber setting | 1,400ºF-1,800ºF (760ºC - 982ºC) |
Retention Time | In excess of 2 seconds. |
Draft | Induced via refractory lined draft inducer. |
Shipping Weight | 53,000 lbs. (24,041 kg) |
Emissions | The Keller Manufacturing Cremation Equipment cremator shall meet or exceed federal, state/province and local environmental regulations. |
Emission Control | Secondary chamber equipped with one, 1,500,000 BTU/HR burner. Also equipped with an electronic exhaust gas scanner system which temporarily suspends operation of the primary chamber burner if the opacity of the exhaust gases reaches the maximum locally authorized level. |
Steel Construction Specifications | |
Structure | The structure to be heavy 3" steel angle, square tube; 3/8" steel plate, seal welded construction. |
Subfloor | Subfloor to be 10 gauge steel plate, seal welded construction. |
Exterior shell | The exterior shell to be 14 gauge steel removable panels. |
Interior shell | Interior shell to be 10 gauge steel, seal welded construction. |
Insulation & Refractory Specifications | |
Hot Hearth | 3000ºF (1650°C) abrasion resistant cast refractory monolithic cast 7" - 13" thick, 1 ½". |
Chamber Floors | 3000ºF (1650°C) abrasion resistant cast refractory, 5" thick on top of 2" 2400ºF (1316°C) light weight insulating castable. |
Chamber Ceilings | 3000ºF (1650°C) cast refractory, monolithic cast, flat roof, 5"-9" thick, topped by 2", 2400ºF (1316°C) lightweight insulating castable. |
Interior Walls | 3000ºF (1650°C) cast refractory 5”. Outer walls backed by 4" (102 mm) of 1900ºF (1038°C) ceramic fiber insulation. |
Stack | Lined with 2-3" (51 to 76 mm) of 2200ºF (1205°C) insulating refractory. |
Skin Temperature Control | Integral dual casing, completely air-cooled design to prevent excessive heat radiation. |
Combustion Equipment | |
Combustion Air | One (1) Single or 3 phase, 208-230/460V, 17-15.5/7.6 amp, 10 hp air blower motor (1,700 CFM (158 CMM) |
Primary Chamber | Four 500,000 BTU/hr. nozzle mix, gas-fired burner; Eclipse, North American, or equal. |
Secondary Chamber | Two 1,500,000 BTU/hr modulating, nozzle mix, gas-fired burner. Eclipse, North American, or equal. Depending on application, one of the burners may be 2.0 MMBtu for States with 1800ºF pre-heat requirement. |
Burner Flame Safeguard | Control supervision on each burner via a flame safeguard relay and ultra-violet light detector. |
Low Air Pressure Safety Switch | Interlocked to all burners. |
Exhaust Gas Temperature Reduction | Exhaust duct operating exit temperature: 900ºF (482ºC) |
Hot Air Duct | 10 gauge carbon steel, high temperature 2-3" (50 – 76 mm) refractory lining, pre-drilled flanges, 28” (711 mm) Outside Diameter, 32" (813 mm) at flanges. |
Utility Requirements | |
Gas | |
Natural Gas Pressure | 12-15" W.C. (304 to 381 mm) (12” Static) |
Propane Pressure | 10-14" W.C. (288-355 mm) |
Flow Rate | Flow Rate: 5,000,000 BTU/hr. |
Electrical | |
Voltage | 220/440 Volts |
Phase | Single or 3 Phase |
Freq. | 50/60 Hz |
Amps | 1 Phase: 70 Amps 3 Phase 230v/40 Amps, 440v/20 Amps |
Documents | |
Specifications | KMA 1200-1000 4C Specifications (PDF) |
Machine Drawings | KMA 1200-1000 4C Drawings (PDF) |
Cremation Accessory Equipment
Complimentary products that simplify and professionalize your process to assure you are applying the industry’s “Best Practices”.
Other Units In This Equipment Line
Our full line of animal cremation equipment will meet or exceed every need your facility has now, and well into the future.